Why Manufacturers Must Invest in Digital Ecosystem to Drive Performance
To continue pushing boundaries and go even faster, manufacturers must invest in the long game by prioritizing the development of their digital ecosystem.
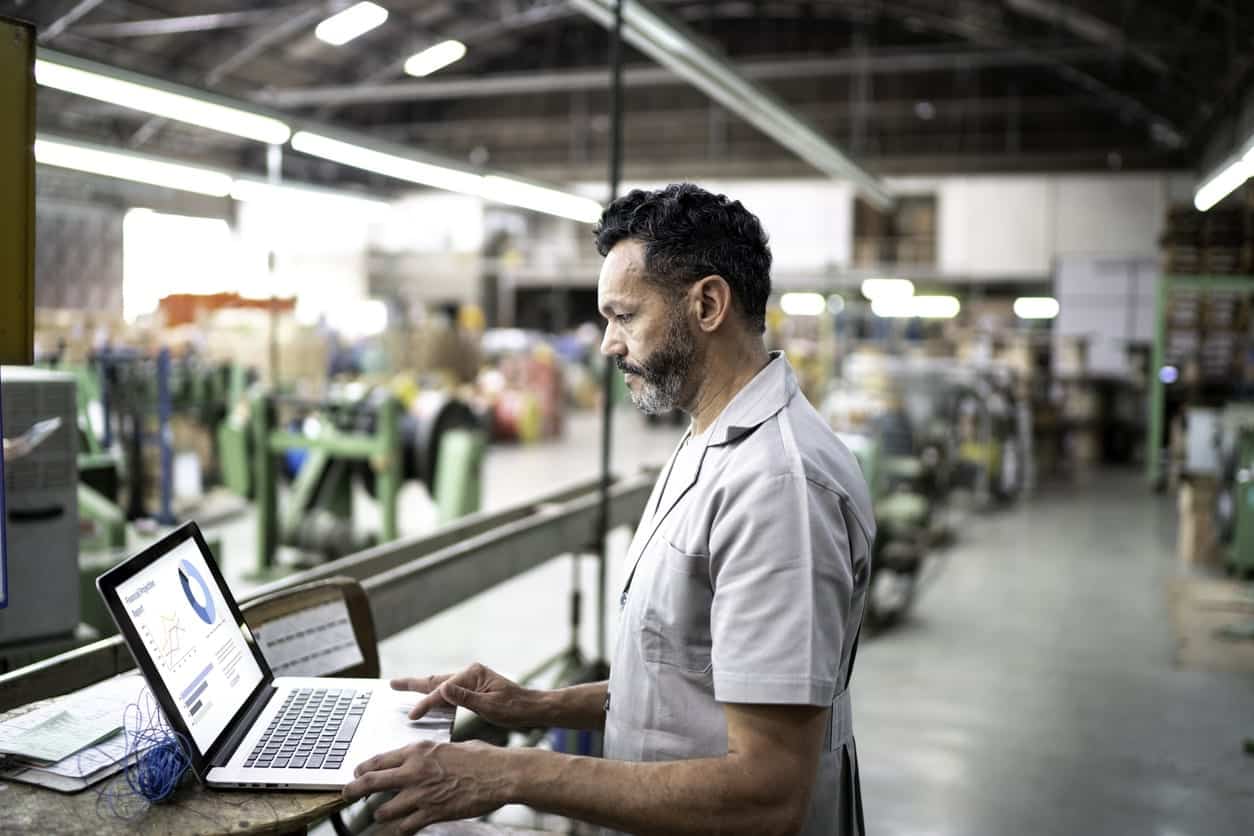
Since the advent of the assembly line, manufacturers have become experts in developing processes that boost efficiency and streamline the factory floor. However, to continue pushing boundaries and go even faster, manufacturers must invest in the long game by prioritizing the development of their digital ecosystem.
According to a report last year from Forrester, only 36% of global purchase influencers in the manufacturing sector consider accelerating the shift to digital business to be a high priority. Instead of transforming how they do business and exchange data, some of these organizations are instead opting for less effective, short-term operational goals that shave only 1%-2% off the cost of an established process.
In order to stay ahead of the competition, even in these current unprecedented and challenging global operating conditions, progressive manufacturers should be at least planning, or working, as best they can, to build their digital ecosystem. They need to enable isolated components of the organization to work in harmony, allowing them to access and act on critical data that can save cost and troubleshoot product issues. Some technology may appear to be fast to deploy, but shows dramatically less ROI over time.
Go Big or Go Home
Manufacturers, like any other digital-first businesses, should first look to adopt data collection and machine learning technologies that can improve communication about and between siloed entities. A complete set of information and real-time data analysis can result in fewer mistakes, greater business value and drive productivity. Daniel Newman, a principal analyst of Futurum Research, explains that smart factories with integrated IT systems provide relevant data to both sides of the supply chain more easily, increasing production capacity by 20%.
Building a digital ecosystem can be a serious overhaul. It requires an abundance of financial resources, leadership commitment and time. However, connecting all the data – from build-out, to logistics, to product design, to customer support – will produce more informed insights, that results in decision-making that has a much larger and longer-lasting impact on the bottom line.
Predict Maintenance Needs To Lower Costs
Standardized maintenance schedules are the norm for most manufacturers. However, plans can quickly deteriorate when machinery degrades unexpectedly, disrupting the schedule and causing even more issues than it did previously. By collecting signals on how different equipment and processes are operating, we can now predict problems before they happen, saving time, money and allowing us to prioritize maintenance schedules accordingly.
For example, Trenitalia, the primary train operator in Italy, has recently adopted connected business processes to capture signals from its trains, analyze the information and predict maintenance needs, to cut down on unanticipated downtime.
According to Trenitalia CIO Danilo Gismondi, a new train can generate 5,000 signals per second, measuring speed, vibration, temperature, location and also the state of every critical component, from wheels and brakes to exterior doors and toilets. Analysis of this data allows Trenitalia to shift from standardized maintenance schedules across an entire class of locomotives, to predictive models potentially optimized for individual members of the fleet. Forrester indicates that Trenitalia aims to cut its euro €1.3 billion maintenance budget by 8% to 10% as a result.
Connect the Supply Chain
However, equipment is simply a part of the puzzle. Processes, systems and people are all factors that can have a significant impact on production. It can be challenging for cross-functional teams to track and accomplish their shared goals. To smooth the flow from design to build to customer, manufacturers should strategically consider technology that allows them to quickly aggregate and analyze data. This will allow them to pinpoint where problems are occurring along any part of the assembly line, sales cycle and customer journey.
Louise Columbus, Principal, IQMS, part of Dassault Systèmes explains: “Machine learning has the potential to bring an entirely new level of insight and intelligence into these teams, making their goals of optimising production workflows, inventory, Work In Process (WIP) and value chain decisions possible.”
Being able to connect the dots sooner is critical to addressing issues. For example, if an error is encountered, like a batch of tainted lettuce being distributed in supermarkets across the country, it is critical to be able to identify the source of the problem as quickly as possible. With AI-powered search and connected data sources, companies are able to quickly identify where the lettuce originated from, what aspects of it were flawed and where exactly they were shipped. Therefore, when a complication arises, companies are able to provide much more targeted recalls, before it snowballs in to a larger problem.
Invest in Digital, From Build to Sale to Support
Digital is not a one-process-at-a-time decision, and is certainly not a small operational shift. It is implementing an entirely new way of doing business, but in a strategic, practical and cost-effective phased way. To develop a winning digital strategy, progressive manufacturers must connect the dots of their digital ecosystem. Consider technology that enables you to connect all the components of your business, analyses data and processes and provides the most critical insights. Placing AI-powered search and digital at the core of your business is the next necessary step towards driving more innovation in manufacturing, and making baby steps, even now, will help drive overall business performance in the long run.
The original version of this article can be found at Industry Europe.
LEARN MORE
Contact us today to learn how Lucidworks can help your team create powerful search and discovery applications for your customers and employees.