How to Make Manufactures More Agile
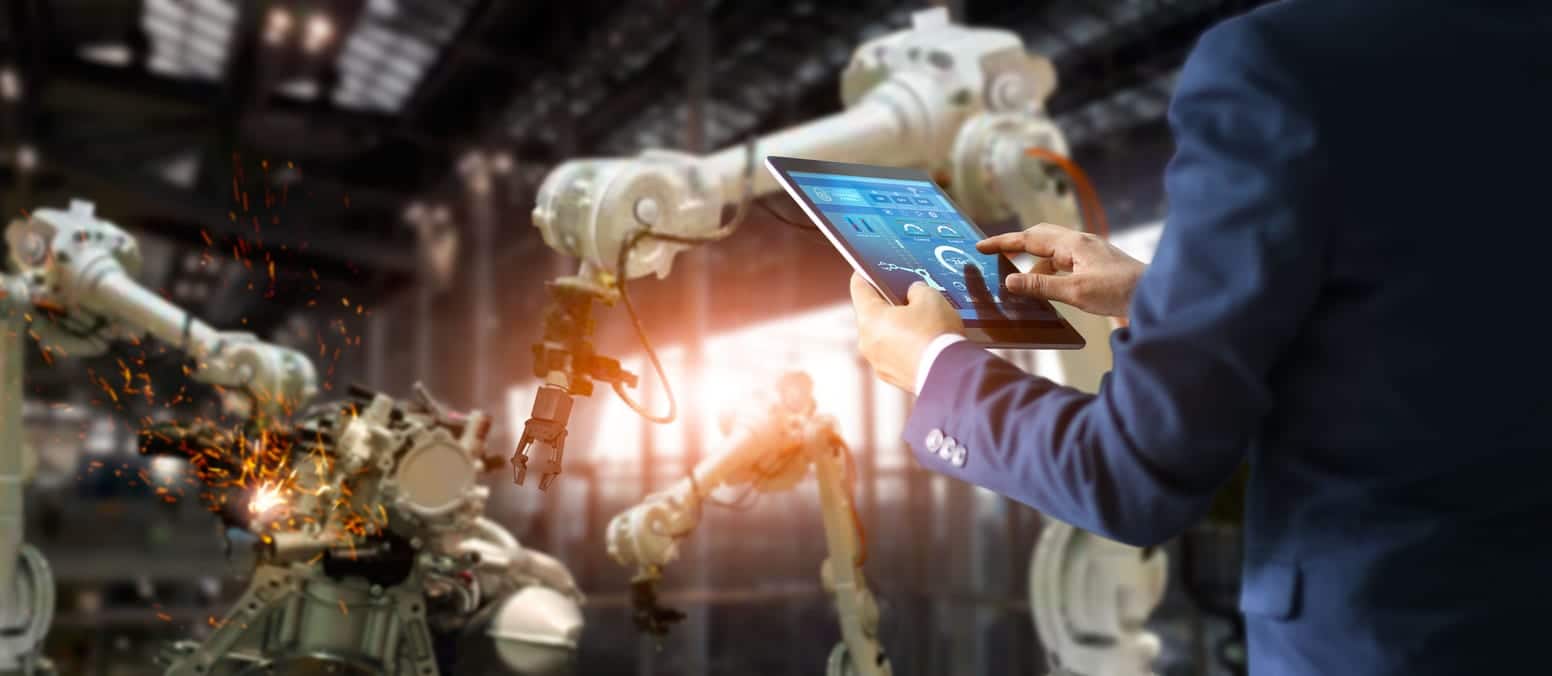
Digital transformation has come to industry at last — with the aim of making every sort of manufacturer more agile and able to respond to marketplace changes.
Evidence of this Fourth Industrial Revolution (4IR), or Industry 4.0, is everywhere from Tesla using artificial intelligence to drive cars, to less visible example of using a 3-D printer to make parts for those cars.
Industry 4.0 may not sound intuitive. Brittanica.com describes the Industrial Revolution as “the process of change from an agrarian and handicraft economy to one dominated by industry and machine manufacturing.” Is Industry 4.0, then, about bringing modern processes to farming and Etsy? Well, kind of.
Industry 4.0 is changing processes, practices, people, culture, equipment, and every other aspect of providing goods and services with the aim of responding to market forces quickly and more easily.
Industry, as we describe it today, is the grouping of organizations based on their primary business activities. There is additional breakdown within that classification of primary, secondary and tertiary industries based on whether a business engages in providing raw materials, using those materials to create other goods, or providing those goods and related services to consumers.
Every business along this change should be participating in Industry 4.0. But that participation may vary greatly, depending on the economic section, the specific goods or services an organization provides, and where the company is in the digital transformation process.
We asked six experts how they define Industry 4.0 and how their companies are investing in the processes.
They said that by using smarter technologies, improving machinery, and using people for problem solving, organizations should see gains in efficiency, have more product reach, find ways to expand, and be better able to serve customers — especially with personalized services.
Industry 4.0 Means Smarter Automation
Industry 4.0 refers to the latest trends in industrial production characterized by the use of interconnected cyber-physical systems (CPS) and advancement in communication systems. Machines are thus able to take physical inputs, calculate a logical decision based on an algorithm, and perform a physical output — entirely without human intervention.
Industry 4.0 currently shows huge potential in the automation and artificial intelligence (AI) space that transcends the usual production applications, including proactive maintenance and overall process improvements. CPS systems can collect historical data and process it to instruct future actions.
Key performance indicators (KPIs) for a successful transition to smarter manufacturing are machine uptime, machine downtime, and mean time between failure. All three KPIs relate to the effectiveness of the equipment which further indicates the health of the manufacturing system as a whole.
Ryan Chan is founder and CEO of UpKeep. In his 20s he saw how maintenance workers struggled to manage their tasks offline. So he learned to code and fixed that problem.
Industry 4.0 Provides Sales Teams With Better Tools
Industry 4.0 is a new era of growth in the tech industry that is marked by intelligence and connection. There are amazing new technologies, such as augmented reality and visual configure, price, quote software (or CPQ) that are hitting the market all at once. These advanced technologies let companies streamline sales and engineering processes to sell and build more, faster. By simplifying processes, sellers can satisfy their customers in a new way by providing a fast and awesome buying experience.
The most noteworthy advancement, which we are seeing during this transformation, is the use of visualization in the sales process. The ability to place a CPQ solution on an external website allows companies to provide a visual of any product on their website or in a sales meeting. With this 4IR technology, potential customers can see exactly what they are purchasing and how much it will cost them in real time. A process that once took businesses several weeks to complete can now be done in a matter of minutes.
Kris Goldhair, Strategic Accounts Director and Co-Founder, KBMax. Goldhair has experience in enterprise sales SaaS and consulting professional with industry expertise in CPQ, 3D product configurators, and B2B2C technology.
Human Workers Are Key to Industry 4.0
The standard definition of Industry 4.0 tends to focus on the rise of automation, robotics and smart technology but omits the role for human workers, who play a pivotal role in the success of advanced technology.
We are living in a dynamic era where unlocking and multiplying human ingenuity is central to manufacturing.
There are opportunities to gain efficiency and improve problem-solving by having better data. By investing in machine integration and the Internet of Things (IoT) sensors for machines, you can gain additional data, but you the data still needs to be aggregated and visualized in a way that humans can quickly identify quickly and prioritize what which issues to address first.
On the manufacturing plant floor, one tech problem can shut down the whole line. By allowing humans to be a part of the equation in real time, tech operates at its fullest capacity, and humans get to keep their jobs.
The human brain is still the most powerful technology on the plant floor. In order to compete, we need to enhance and foster natural intelligence more than we need artificial intelligence.
Keith Barr, CEO and President of Leading2Lean, pioneer in high tech, customer relationship management and manufacturing markets.
Industry 4.0 Includes Personalizing Consumer Products
In an ever-changing technology landscape, manufacturers and machine shops have the opportunity to add new tools to increase efficiency but face the challenge of choosing tech that can scale modernization reliably and cost-effectively.
One successful example is 3D printing which can work well alongside older workflows. Given the low cost, it can also replace old machinery.
Automated 3D printing solutions are already helping scale personalized products for mass market opportunities such as patient-specific models in healthcare to consumer products such as dentures, shoes, and earbuds. New Balance uses 3D printers for custom footwear manufacturing. Dentists create custom-fitted dentures with 3D printers, and healthcare facilities can 3D print body parts to let surgeons practice on before surgery. That’s just the beginning.
Andrew Edman, Formlabs’ Industry Manager of Product Design, Engineering, and Manufacturing. He is a seasoned designer with deep experience in product development from earliest concepts, product specs, and research, through to DFM/A and scale manufacturing.
Smart Manufacturing Includes IoT
Smart factories combined with cloud infrastructure that uses IoT to automatically connect every person and machine together in a bi-directional feedback loop connects the factory floor with customers via a single digital thread to ensure quality, delivery, speed, and accuracy.”
For example, software-powered automation can improve production processes of printed circuit board assembly (PCBA) prototypes and save design time, build cost, and lead time.
This process helps employees optimize their time by telling them where to be, when, and what step in the process needs their attention. Moreover, using IoT networked devices to connect every person with every machine, streamlines operations, improves collaboration, and simplifies remote management and control.
Shashank Samala, co-founder and VP of Product at Tempo Automation, electronics manufacturer for prototyping and low-volume production of printed circuit board assemblies.
Key to Industry 4.0 Is Automation and Connectivity
Focusing on automation of the part sourcing process makes manufacturers more cost competitive and reduces their time to market. AI-powered tools instantly can predict the cost and lead-times of manufacturing for 3D printing, computer numerical control (CNC) machining, and injection molding. Creating a global network of connected manufacturing services, the smartest manufacturing network on the planet, will optimize the global supply chain.
Filemon Schoffer, Co-founder & COO, Hubs, with a background in both Physics and Industrial Design Engineering Filemon aims to contribute in moving the 3D printing industry forward.
Evelyn L. Kent is a content analytics consultant who specializes in building semantic models. She has 20 years of experience creating, producing and analyzing content for organizations such as USA Today, Tribune and McClatchy.
LEARN MORE
Contact us today to learn how Lucidworks can help your team create powerful search and discovery applications for your customers and employees.